
Copper Ore Crushing, Grinding & Flotation
The attraction of semiautogenous grinding in copper operations is that they can accommodate ores that are hard or soft, wet or dry, sticky or otherwise. The SAG mill can handle everything that is presented to it, regardless of coarseness or fineness, or hardness or moisture content, and Copper Sulfide Flotation Mineral Processing & Metallurgy,Copper Rougher Flotation For large tonnage circuits normally encountered in many of the copper operations the open or free flow type “SubA” Super Rougher Flotation Machine is Copper Flotation Mineral Processing & Metallurgy,A Copper Flotation Flowsheet. Because the copper in this type of ore usually assays only plus or minus 1% copper, the porphyry copper operations must be relatively large in order to be
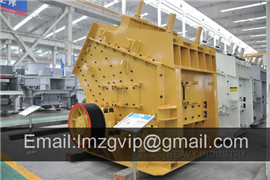
Copper Flotation, Extraction of Copper, Copper Xinhai
The dewatering of copper, lead and zinc concentrates used Xinhai efficient deep cone thickener + ceramic filter. The concentrate moisture was about 12% after dewatering. Process Indicator: electrical mining grinding flotation copper,It houses conventional crushing, grinding, and flotation circuits to produce the copper‐gold concentrate. The run‐of‐themine (ROM) ore material undergoes primary crushing in an Copper Flotation: Effects of Particle Size, Grinding and ,Concerning grinding time, the initial sample grinded in five different time periods (20, 22, 24, 26, and 28 min), and the products subjected to flotation experiments. Also, flotation tests.
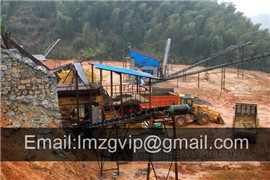
Grinding ABB Mining
Grinding is a significant and critical part of the ore winning process. On average, milling is the process that requires the most energy in the whole mining operation. To ensure profitable Grinding and Flotation Optimization Using Operational ,The objective of copper flotation is typically to maximize the dollar return on the concentrate produced while minimizing the energy and other consumables. It is also essential to minimize Flotation Mineral Processing & Metallurgy,The Arizona Copper Co.’s plant will treat the slime and recrushed sand from previous gravitytreatment; out of an original tonnage of 4000 there will be about 3600 tons of flotation feed.

Electrical Mining Grinding Flotation Copper
Mineral Processing Copper Ore Electrical Motor Flotation Machine. Our Services Aftersales service LUOYANG ZHONGTAI INDUSTRIES able to provide: 1. ENGINEERED SPARES A study of the effect of grinding environment on the ,615 Procedure 1: Wet milling followed by lime addition in the flotation cell • Procedure 2: Wet milling with lime addition in the mill • Procedure 3: Dry milling followed by lime addition in the flotation cell These procedures are shown in Fig. 2 Increasing the grind size for effective liberation and ,81 Furthermore, Sahyoun et al. (2005) conducted flotation tests on the same ore and demonstrated a 3–6% increase in copper recovery after microwave treatment (up to 12 kW and 1.7 kW h/t on <22 mm size material) as opposed to the 1% increase reported by Kingman et al. (2000a), attributed to the higher power density sustained in the single mode cavity.
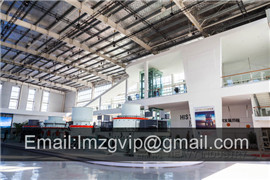
The effect of grinding conditions on the flotation of a
2003111 The grinding conditions affect significantly the subsequent flotation stage of this sulphide copper ore. The presence of iron ions in the slurry is deleterious to the flotation of copper minerals and may be avoided by the utilisation of lined mills and nonferrous or corrosion resistant grinding media, such as stainless steel or pebbles.Grinding and Flotation Optimization Using Operational ,111 The objective of copper flotation is typically to maximize the dollar return on the concentrate produced while minimizing the energy and other consumables. It is also essential to minimize the nonproductive time that the process units are meeting production targets.What is Flotation in Sulfide Copper Extraction? miningpedia,527 The firststage grindingflotation process is suitable for the treatment of ore with coarse and uniform copper minerals embedded in particle size, loose binding of copper minerals and gangue, and smooth and flat contact edges.
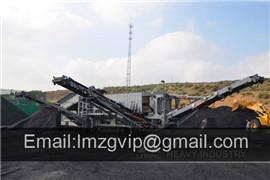
A review of the effects of the grinding environment on the
201178 All other things being equal, once the pulp potential reaches the threshold level necessary for flotation, copper sulphide minerals generally float well, and as such, their floatability is independent of the previous grinding conditions. 2.2. Effect of galvanic interactions between sulphide mineralsFutureproofing the world’s copper supply International ,525 Flotation is a complicated physicochemical process where reagents such as frothers, collectors and pH modifiers are introduced to promote separation. The flotation feed can vary in particle size and chemistry depending on how the grinding circuit is optimised, and may contain excess fines.Copper Mining and Extraction Copper Mining ,1116 Liquid solutions are used in these processes to extract and purify copper from copper oxide ores at ordinary temperatures, in three major steps: 1) heap leaching to leach out metals, 2) solvent extraction to separate
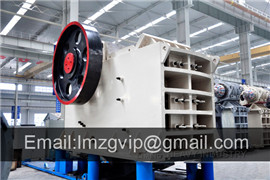
Copper Lead Zinc Mining Mineral Processing & Metallurgy
1121 The mill consists of a single stage crushing, single stage closed circuit grinding, flotation of a copper concentrate in the unit cell, flotation of copperleadsilver concentrate, and flotation of a zinc concentrate. The bulk copperleadsilver concentrate is then subjected to reflotation using cyanide to depress the copper and float the lead.Recovery of Copper from the Slag of Khatoonabad Flash,201365 At the grinding rate of 85 % −74 μm, a significant change in the recovery of copper was observed, and at the flotation time of 14 min, a 90.6 % recovery of copper was obtained. By increasing the grinding to the extent of 93 % −74 μm, no significant change occurred in the copper recovery, and the grade and recovery of copper were recordedCopper Flotation: Effects of Particle Size, Grinding and ,2010106 In the current research work, influences of particle size, grinding time, and agitation rate on the flotation of a copper sample from Sungun copper mine (E. Azerbaijan, Iran) containing 0.66% Cu

(PDF) A Review of the Flotation of Copper
74 S. Bulatovic, "Flot ation of Oxide Copper an d Copper Cobalt Ores," in Handbook of Flotation R eagents: Chemistry, Theory and Practice Volum e 2, Elsevier Science a nd Technology Books,2010, pp60 Centuries of Copper: The Flotation Process,53 The powdered product of grinding the ore is fed into a series of tanks called flotation cells which are filled with a solution containing various oils capable of forming a froth. Air is pumped into each cell, the solution being agitated to bring froth of bubbles to the surface. In the case of copper minerals, the particles adhere to this frothCopper Mining and Extraction Copper Mining ,1116 Copper is extracted in large amounts from the Earth’s crust by mining of sulphide ores and also oxide ores. Studies reveal about 80% of copper is produced by its extraction from sulphide ores. Chalcopyrite is a certain kind
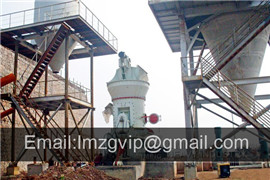
Estimated Water Requirements for the Conventional
201253 This report provides a perspective on the amount of water used by a conventional copper flotation plant, including the makeup water required to compensate for water losses. Much of the global supply of copper originates from mines that also produce byproduct molybdenum, but for simplicity, a single copper concentrate has been modeled for thisEnergy and Environmental Profile of the U.S. Mining ,2013118 5.1.1 Copper Ore Mining Copper is commonly extracted from surface, underground and increasingly, from in situ operations. In 2000, the principal mining States, in descending order, Arizona, Utah, New Mexico, and Montana, accounted for 99 percent of domestic production. Copper was also recovered at mines in three other States.Effects and Mechanism of Different Grinding Media on the ,1029 It was found that the copper flotation recovery after using a selfgrinding machine was higher under the same flotation feed size. Recently, Li et al. [ 16] investigated the surface properties and flotation behavior of scheelite particles produced by ball and rod mills.

GE Power Conversion Industry Mining GE Power
1124 GE Power Conversion builds highly efficient motors, drives and integrated system solutions for the mining industry. Our electrification and automation solutions help you to achieve higher throughput and recovery with lower maintenance and energy costs. Combining electrification technology with project life cycle services and digital capabilityMinerals Free FullText Investigating the Influence of the,1018 Flotation is an electrochemical process comprising many interdependent conditions that are difficult to decouple in terms of controlling flotation performance. The extent of electrochemical activity is mineral dependent and can be measured against a reference cell to differentiate between minerals.Futureproofing the world’s copper supply International ,525 Flotation is a complicated physicochemical process where reagents such as frothers, collectors and pH modifiers are introduced to promote separation. The flotation feed can vary in particle size and chemistry depending on how the grinding circuit is optimised, and may contain excess fines.
- Cement Plants For Sale In Mauritania
- شراء حزام ناقل في سنغافورة
- manual book of cone crusher
- كسارة خام الحديد المتنقلة السعر مصر
- التعدين تخطيط الكرة مطحنة
- الفحم محطة كسارة 500 الهيدروكربونات النفطية
- كسارة vsi لصنع الرمل لفلسبار
- tantalite ore crusherfeldspar
- الشركات المصنعة لآلة المطحنة في مصر
- بيع طن من كسارة الحجر للساعة الواحدة
- نموذج خطة عمل للأحجار المسحوقة
- alquiler trituradoras compania
- crusher conveyor manufacturers in india
- كسارة فكية شبه محمولة أكبر
- Buy Poultry Feed Mill Machinery In Pakistan
- دليل مطحنة الكرة الصغيرة
- المحمولة تأثير محطم بيع
- كيفية تصميم آلة مطحنة الكرة الذهبية
- الآلات الخبث سحق في المملكة العربية السعودية
- كسارة مخروطية ماركة مصر