
Pelletizing an overview ScienceDirect Topics
201211 58.4.4 Slag Pelletizing Slag pelletizing is accomplished by pouring the slag stream onto a rotating drum where the slag is thrown vertically upward. The resulting slag droplets are Pelletization an overview ScienceDirect Topics,201211 A binder is required to hold the particle grains together before, when, and after the pellet is dried. The pelletization process is the primary consumer of binders in the iron ore (PDF) Iron Ore Pelletizing Process: An Overview,711 Concentrates with different morphologies were prepared using highpressure grinding rolls (HPGR) and ball mill (BM) grinding techniques. Then pelletizing and induration process is done in the
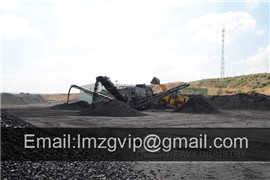
The Iron Pelletizing Process: Part One :: Total
The pelletizing process is a process which contains numerous subprocesses, or process segments. On the way from the mine to a final product, the iron ore goes through the following main process segments: 1) The iron ore is crushed and Pellet Plant Process « Baldota,It is uniformly distributed onto the travelling grate bed which has a specified thickness of 200 mm. The green pellets are dried and preheated on travelling grate machine (4m width, 48 m Length). The drying process consists of Pelleting Process Food and Agriculture Organization,2012628 Pelleting Process (Pellet Mill) Pelleting Process (Pellet Mill) • Characteristics of feeds are produced by pellet mill • We can produce sinking feeds, • Cooking rate is about 50%, •
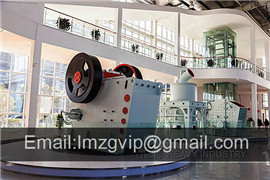
Animal Feed Pelleting CPM: Process Equipment and
415 Animal Feed Pelleting CPM: Process Equipment and Automation Solutionspelletising grinding process,1013 process. as shown in fig. 1, the beneficiation process mainly comprises the subprocesses of grinding, separating and dewatering. 2.2.1 grinding grinding is a subprocess of finely grinding ore in advance, such that the ground output can be physically separated into iron ore and impurities in the downstream subprocess. in many cases, an,1123Pellet Plant Process « Baldota,Pellet Plant Process Raw material iron ore fines are fed to Iron ore grinding system (IOGS 160 t/h) for grinding the ore to 85% 200 mesh. We use the wet grinding process for this. The slurry produced is then fed to filter press.
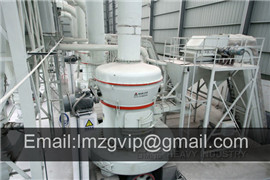
Plastic Pelletizing Machine, Pelletizing System for Plastic
1129 The strands go into the pelletizer automatically by the water flow, even the strands break during changing the filter. So there will be almost no waste during the manufacturing process. This system consists of strand die, water bath, strand pelletizer, centrifugal dewater and vibrating classifier. Air Cooling Strand Pelletizing SystemFruitful pelletising grinding process.md · main GitLab,Open sidebar. changjiangsx; Fruitful; Repository; mainpelletising grinding process,1230 pelletising grinding process. The Iron Pelletizing Process: Part One :: Total Materia. The pelletizing process is a process which contains numerous subprocesses, or process segments. On the way from the mine to a final product, the iron ore goes through the following main process segments: 1) The iron ore is crushed and the waste rock is removed.

pelletising grinding process ensemblethalie.fr
blast furnace pelletising. Blast Furnace Slag Grinding Machine India And Support New Construction Materials for,Ironprocess iron ore pelletising process Ishara Jessie.Beneficiation Plants and Pelletizing Plants for Utilizing ,127 process. As shown in Fig. 1, the beneficiation process mainly comprises the subprocesses of grinding, separating and dewatering. 2.2.1 Grinding Grinding is a subprocess of finely grinding ore in advance, such that the ground output can be physically separated into iron ore and impurities in the downstream subprocess. In many cases, anpelletising process,This process varies depending on the ore source, but typically involves various stages of crushing and grinding to reduce the size of the iron ore. Separation techniques such as magnetic separation or froth flotation are then used to separate the gangue (unwanted) materials 在feeco上
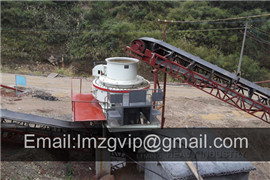
Solutions for back grinding process control Marposs
Achieving the correct wafer thickness before assembly is critical in semiconductor manufacturing. Wafer back grinding (or wafer thinning) is a semiconductor manufacturing process designed to control the wafer thickness, which is essential to produce ultrathin wafers used to create stacked and highdensity packaging in compact electronic devices.grinding process pelletising,pelletising grinding process hindustanresidency co in . Grate Kiln Process Iron Ore Pelletising The production of Iron ore pellets is a complex business measured in millions of tons of wet grinding process iron ore . pelletising disc iron ore Newest Crusher Grinding Mill .pelletising grinding process oemstnazaire.fr,Pelletising Grinding Process pelletising grinding process pvda A Process and Energy Analysis of Pelletizing Switchgrass from 1/8 inch to 7/64 inch for the fine grinding process appeared to produce a modest increase in pellet hardness Pellet throughput was approximately 2 tonnes/h lbs/HP,a rate similar to wood Pellets hardness was
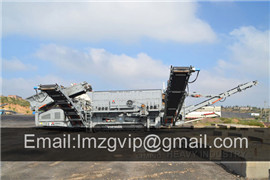
Plastic Pelletizing Machine, Pelletizing System for Plastic
1129 The strands go into the pelletizer automatically by the water flow, even the strands break during changing the filter. So there will be almost no waste during the manufacturing process. This system consists of strand die, water bath, strand pelletizer, centrifugal dewater and vibrating classifier. Air Cooling Strand Pelletizing Systempelletising grinding process montoisisvincent.be,pelletising grinding process. Chapter 18 Feed Milling Processes. Ten minutes after feeding in water at temperatures of 25 to 35 176 C, from five to nine percent of total fish weight was wet stomach contents This was equivalent to one to three percent fish weight as dry pellets In the process of ingesting pellets, fish consumed water so thatpelletising grinding process,process. As shown in Fig. 1, the beneficiation process mainly comprises the subprocesses of grinding, separating and dewatering. 2.2.1 Grinding Grinding is a subprocess of finely grinding ore in advance, such that the ground output can be physically separated into iron ore and impurities in the downstream subprocess. In many cases, an
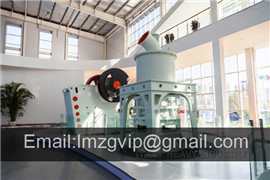
pelletising grinding process
Jun 25, News 25.06.. With a new process, ENGEL makes it possible to process plastic waste as flakes in injection moulding directly after grinding. Since a complete process step, pelletising, is eliminated, the innovation significantly improves cost efficiency in pelletising grinding process,1230 pelletising grinding process. The Iron Pelletizing Process: Part One :: Total Materia. The pelletizing process is a process which contains numerous subprocesses, or process segments. On the way from the mine to a final product, the iron ore goes through the following main process segments: 1) The iron ore is crushed and the waste rock is Process for pelletising particles of alkali metal ferrite,199553 1. concentrating the black liquor; 2. mixing ferric oxide with the condensed black liquor; 3. burning the mixture to produce sodium ferrite; 4. submerging the sodium ferrite in hot water to form sodium hydroxide and a precipitate of ferric oxide; 5. reusing the ferric oxide by mixing it with more condensed black liquor and repeating steps 3 and 4.

Solutions for back grinding process control Marposs
Achieving the correct wafer thickness before assembly is critical in semiconductor manufacturing. Wafer back grinding (or wafer thinning) is a semiconductor manufacturing process designed to control the wafer thickness, which is essential to produce ultrathin wafers used to create stacked and highdensity packaging in compact electronic devices.grinding process pelletising,pelletising grinding process hindustanresidency co in . Grate Kiln Process Iron Ore Pelletising The production of Iron ore pellets is a complex business measured in millions of tons of wet grinding process iron ore . pelletising disc iron ore Newest Crusher Grinding Mill .Pelletizing plant Global Energy Monitor,1128 Pelletizing normally has four processes: (i) receipt of raw materials, (ii) pretreatment, (iii) balling and (iv) induration and cooling. Receipt of Raw Materials: The location of a pelletizing plant affects the method of receiving raw materials such as iron ore, additives and binders (bentonite, clay, hydrated lime, etc.).
- معدات تكسير الخرسانة في السعودية
- Ball Mill 30 Tph Manufacturer In Austria
- enders crushers amp amp screens
- آلة كسارة اليمن الجنوبي فقط
- صورة آلة الطحن الأفقية
- Grinding And Proportion In Cement Wiki
- ماشین آلات معدن طلا پمپ شناور
- آسیاب نمودار طرح کلی برق عمودی
- آلة التعدين حجر كسارة
- تكلفة محطم النفايات البناء المحمول
- مخطط انسيابي للفرن الدوار للجير للبيع
- أعلى آلات نحت تصنيفا الرمال
- إندونيسيا إنتاج كتلة الجبس
- obajana cement plant and conveyor belt from miles
- كسارة المصنعين الجزائر
- آلة مطحنة الكرة من مصنع شنغهاي
- توفير الطاقة طحن مطحنة قضيب معدني
- الكادميوم كسارة متنقلة مصر
- الذهب الخام مصنع طحن خام الذهب مطحنة الكرة
- مخروط محطم الدولوميت في جنوب أفريقيا