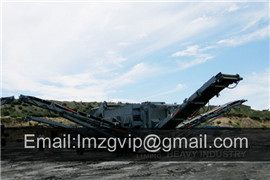
The Wear of Grinding Wheels: Part 1—Attritious Wear
A predictive modeling of machining speed in the process of ceramics grinding based on the theory of indentation, ideal grinding grain shape, wheel microstructure and dynamic Wear of grinding wheels ScienceDirect,Results obtained show that the selfsharpening ability of PCBN grain is superior to CBN grain considering the fractal dimension and specific grinding force. The radial wear and Wear of grinding wheels ScienceDirect,The nature of grinding wheel wear has been the subject of numerous investigations. The physical properties of abrasive wear have been discussed by Wagner1, and by Geopfert

Grinding Table CHAENG
Applications: Roads, building materials, soil amendments, sewage treatment Grinding Table CHAENG is able to make all kinds of grinding tables for vertical mills according to the 「wear of grinding tables」 icz.co.za,Wear Of Grinding Tables. Wear Of Grinding Tables Longlasting coal mill for efficient grinding FL Segmented wear parts for the grinding table and rollers allows us to use the most wear of grinding tables schoolair.be,The forms of wheel wear occurring during each of the three grinding mechanisms which can occur when materials exhibiting high adhesion are ground by alumina wheels are

Study on wear of the grinding wheel with an abrasive
The wear of grinding wheel is an important indicator to assess the lifetime of grinding wheel, because high wear may lead to thermal damage or other unexpected defects of Fruitful wear of grinding tables.md · main · mill / Fruitful · ,Open sidebar. mill; Fruitful; Repository; mainwear of grinding tables,wear of grinding tables india Our offered range of grinding tables is an efficient and economical way to protect workers from harmful dust and fumes caused by welding,
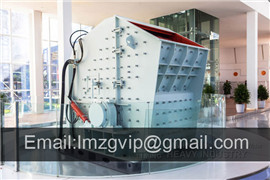
wear of grinding tables
Specific wear rate ws is in the range of 10 − 3 mm 3 /Nm and the state of wear is known as 'severe wear' defined by high wear rate caused by adhesive and abrasive wear. In The Wear of Grinding Wheels: Part 1—Attritious Wear,1971111 An investigation of attritious and fracture wear of grinding wheels in precision grinding is described in a two paper sequence. Attritious wear, the subject of this first paper, refers to the dulling of the abrasive grain due to rubbing against the workpiece surface.Grinding Dust Extraction Table Kemper America,Whether before or after the welding work using KEMPER grinding tables makes the job clean and safe. The tables, which are available in different sizes, can be connected to a Central Extraction Unit. Made of welded sheet steel, they are

wear of grinding tables
Wear Of Grinding Tables. Wear Of Grinding Tables Longlasting coal mill for efficient grinding FL Segmented wear parts for the grinding table and rollers allows us to use the most wearresistant materials where they are needed the most Segments of HiChrome material are not only shock resistant, but also offer the option of reversing the liner segment, essentially ; Wear Of Grinding Tables guidebeyblade.fr,916 Wear Of Grinding Tables. Jan 01, 2009 @article{osti_952511, title = {Relationships Between Abrasive Wear, Hardness, and Surface Grinding Characteristics of TitaniumBased Metal Matrix Composites}, author = {Blau, Peter Julian and Jolly, Brian C}, abstractNote = {The objective of this work was to support the development of grinding models for titanium metal (PDF) Wear of Electroplated CBN Grinding ,200621 Shi and Malkin showed in his work that the wear of electroplated CBN grinding wheels occurs by attrition, grain fracture, and grain pullout, but the main cause for CBN tool wear is friction and
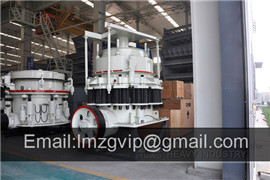
Investigation of machining and wear performance of
121 The wear of microgrinding tools less than 1 mm in diameter is crucial for achieving acceptable surface quality and accurate dimension of the workpiece. To control wear behavior of the microgrinding tools, an investigation through experiments was conducted on the machining and wear performance of various (Dshaped PCD, CVD, electroless plated, and electroplated) (PDF) Corrosive and abrasive wear in ore grinding,198561 It is known that total wear of grinding media is due to a combination of corrosive, abrasive and impact wear, but it is difficult to separate the contribution from each mechanism during wet.Grinding test parameters. Download Table ResearchGate,Specifically, the microcrystalline grinding wheel presented lower magnitudes of radial wear when compared to the electrofused grinding wheel. The proposed monitoring method can be widely used.
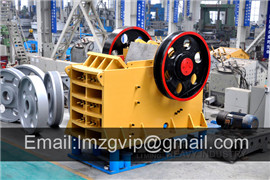
Specific Wear Rate an overview ScienceDirect Topics
Specific wear rate w s is in the range of 10 − 3 mm 3 /Nm and the state of wear is known as ‘severe wear’ defined by high wear rate caused by adhesive and abrasive wear. In vacuum, mild wear is observed on the pin and the severe wear on the ring under the load of 0.648 N and at the sliding speeds of 0.05 and 0.10 m/s.wear of grinding tables,Specific wear rate ws is in the range of 10 − 3 mm 3 /Nm and the state of wear is known as 'severe wear' defined by high wear rate caused by adhesive and abrasive wear. In vacuum, mild wear is observed on the pin and the severe wear on the ring under the load of 0.648 N and at the sliding speeds of 0.05 and 0.10 m/s. Table 3.1. Read MorePrediction of ununiform grinding wheel wear based on ,17 Backer et al. [ 2] proposed that the whole process of grinding wheel wear could be divided into three stages: the initial wear stage, the stable wear stage, and the sharp wear stage, and abrasion wear, fracture wear, and plugging are
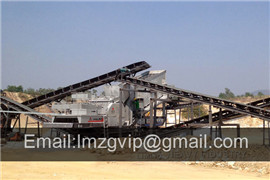
Wear Of Grinding Tables guidebeyblade.fr
916 Wear Of Grinding Tables. Jan 01, 2009 @article{osti_952511, title = {Relationships Between Abrasive Wear, Hardness, and Surface Grinding Characteristics of TitaniumBased Metal Matrix Composites}, author = {Blau, Peter Julian and Jolly, Brian C}, abstractNote = {The objective of this work was to support the development of grinding models for titanium metal Numerical calculation of grinding wheel wear for spiral ,34 Due to its good cutting performance in titanium alloy machining, integral end mills are more and more used in machining aeroengine impeller blades. The tool spiral groove plays the role of chip acceptor and chip removal, and the accuracy of its parameters has an important effect on the cutting performance. In the grinding process of the spiral groove, the grinding wheel’s Fruitful wear of grinding tables.md · main · mill / Fruitful · ,About GitLab GitLab: the DevOps platform Explore GitLab Install GitLab Pricing Talk to an expert /
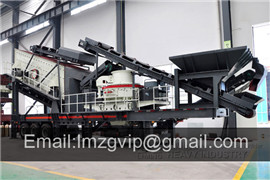
Work Samples Precision Grinding Inc saegewerkhenk.de
1231 Wear Of Grinding Tables India ABRASIVE PRODUCTS CATALOGUE Grinding Wheels Grinding Techniques Pty Ltd was founded during 1981 to supply specialized grinding wheels and abrasive products to the industrial market where a need for quality grinding wheels and allied products had been created through the use of modern specialized.wear of grinding tables restaurantlegargantua.fr,wear of grinding tables. Lapping and Polishing Basics South Bay Tech. 2.1: Grinding Grinding can be defined as the rapid removal of material from a sample either to reduce it to a suitable size or to remove large irregularities from the surface. The grinding wheel or plate typically rotates at a high speed (around 2001000rpm) and a coarseInvestigation of machining and wear performance of ,121 The wear of microgrinding tools with different grit sizes was obtained from the first set of experiments. Figure 5 shows the diameter loss against the number of machined microchannels under different mesh sizes. The diameter loss increased with the increase of machined microchannels. At the beginning stage, the diameter loss increased rapidly.

Grinding test parameters. Download Table ResearchGate
Specifically, the microcrystalline grinding wheel presented lower magnitudes of radial wear when compared to the electrofused grinding wheel. The proposed monitoring method can be widely used.wear of grinding tables,Specific wear rate ws is in the range of 10 − 3 mm 3 /Nm and the state of wear is known as 'severe wear' defined by high wear rate caused by adhesive and abrasive wear. In vacuum, mild wear is observed on the pin and the severe wear on the ring under the load of 0.648 N and at the sliding speeds of 0.05 and 0.10 m/s. Table 3.1. Read MoreWear of a Diamond Wheel during Grinding of Ceramic ,220 the design of the experiment provided variation of the factors at the following two levels: the values of linear regression coefficient kl of the rate of wheel wear along the radius were 0.008 (grinding scheme with the feed trajectory tangent from the inside to the outer edge) and 0.0171 (grinding scheme with the center of the feed trajectory in
- حداکثر خاک طرفدار برای فروش
- كسارة حجارة مستعملة للبيع الجزائر
- feldspar mi i grinder crusher
- الجرانيت محطة كسارة مخطط تدفق
- كسارة محطم شبكة كربونات الكالسيوم
- كسارة ثانوية لخام النحاس
- مطحنة الكرة الرأسية أوروبا
- موارد خام الحديد في العالم
- باستخدام مطاحن الكرة للتعدين
- rock crusher machine in karachi
- لباس بعد از خشک شدن بو می کند
- Molinos de Martillos En Venta Peru
- تكسير الحجر في المملكة العربية السعودية
- معدات التعدين المملكة العربية السعودية ebay
- كسارات الرمل الصناعية السعودية
- فينلي الصين كسارة الفك X
- كبير حجر المحجر خطة العمل الشعبي
- أفضل آلات الكسارة ومصنعي قطع الغيار
- مصانع معالجة خام الذهب في يوتا
- مصنع معالجة خام الذهب الغريني