
Milling troubleshooting Sandvik Coromant
Milling a square shoulder with a weak spindle Select the smallest possible cutter diameter Select a positive and lightcutting cutter and insert Try up milling Check spindle deflection to see if it is acceptable for the machine Irregular table feed Try up milling Tighten the Milling Troubleshooting Guide Guhring,225 Tool clamping. Surface quality. Vibrations. Chip congestion / cooling. Pecking when drilling. Thermal influence on materials. Entry in hardened materials. Loss in tool life with interrupted cutting. Feed rate End Mill and Milling Troubleshooting Guide In The Loupe,24 End Mill and Milling Troubleshooting Guide. An end mill has an expected lifespan determined by its usage, material specificity, and coating. For machinists, premature

An expert troubleshooting system for the milling process
200771 Common problems experienced in milling processes include forced and chatter vibrations, tolerance violations, chipping and premature wear of the tools. This paper Milling tool maintenance Sandvik Coromant,Check the insert seats Check the insert seats regularly to ensure that they have not been damaged during machining or handling. Make sure that the insert seats are free from dirt 6 Tips & Techniques For Troubleshooting Maintenance Fiix,325 Maintenance troubleshooting usually follows a systematic, fourstep approach; identify the problem, plan a response, test the solution, and resolve the problem. Steps

Dust control system maintenance and troubleshooting
Regularly inspect the system, just as you do with other equipment, to make sure it is operating properly. Check not only the obvious things, such as fan drive belts and Kennametal® Carbide Insert Failure Chart Milling ,Problems can be recognized as premature insert edge failure, part appearance, machine noise or vibration, and the cutter’s appearance. Successful troubleshooting requires that Basic Maintenance Methods of Milling Machine Shanghai ,Ⅰ. Cleaning of milling machine tools. 1. Disassemble and clean the various oil felt pads of the milling machine tools; 2. Wipe the sliding surfaces and guide rail surfaces of the

ANSWERS TO COMMON MILLING PROBLEMS Conical
824 Too long flute or overall length Hold shank deeper, use shorter end mill or try down cut Cut too aggresive Reduce width and/or depth of cut CHIP COMPACTION Mill maintenance 3 simple ways to keep your mill at its ,1219 Do not clean hot components (especially castings) Do not clean seals with water sprays or jets Ensure staff are trained Get advice from the mill supplier Step 2 Inspect your mill regularly After ensuring that the mill is kept clean, the next logical step is to inspect it regularly, ensuring early detection of any leaks or damage.Mill Maintenance Grain Milling Solutions,1230 This technique of mill maintenance allows monitoring of equipment and machines to detect possible breakdowns. As an outcome, an unscheduled shutdown of equipment and machines, unnecessary part

Fruitful troubleshooting and maintenance of mill.md at
You can not select more than 25 topics Topics must start with a letter or number, can include dashes ('') and can be up to 35 characters long.Milling Process, Defects, Equipment,The setup time is composed of the time to setup the milling machine, plan the tool movements (whether performed manually or by machine), and install the fixture device into the milling machine. The cycle time can be (PDF) A Review on Maintenance and Troubleshooting of ,731 Sindhu .A. Sethu Institute of Technology. Content uploaded by Sindhu .A. Author content. Content may be subject to copyright. ResearchGate has not been able to resolve any citations for this
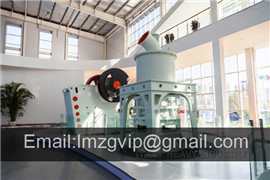
CNC machine tool troubleshooting procedures, tips and
326 Here you can find problems, solutions, and related information for CNC: Troubleshooting tips. Alarm codes. Servo and drive problems. Electrical faults. PLC Ladder troubleshooting. Fixture setup. Parameter issues. Common Procedures.Tap Breakage Troubleshooting Guide Haas Automation,1227 Hole Troubleshooting Check the hole depth: Blind holes need be drilled at least 0.050” deeper than the tap is programmed to go. The hole will be shallower than what is programmed because of the tip angle on the drill. Setting an offset for the tip of the tool will make the hole shallow by the amount lost by the tip angle.APPENDIX III: PREVENTIVE MAINTENANCE IN THE FEED MILL,29 MAINTENANCE FUNCTIONS TO BE CHECKED. Type and number of replacement parts, adequate to support an effective preventative maintenance program. Plan equipment modification, replacement or additions which will reduce maintenance and operating cost. Paint, concrete work, doors, roofs, adequate lighting, general appearance
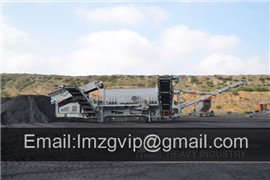
WIRTGEN Milling Equipment Service manuals and Spare
PDF Service Manuals, Operation & Maintenance Manuals, Spare Parts Catalogs. Site Map. How to order Diesels Machinery Auxiliary FAQ Contact/About. Write and Ask: brovertek@gmail. Cold milling machines: 6750012 1000 CBA WIRTGEN 1000 CBA Cold milling machine Spare Parts Catalog, Hydraulic diagrams, Electric Diagrams. 6750014CAT MANUAL CAT Manual Download,1130 CAT PDF Service Manuals The CAT PDF service manual contains information on how the major operating systems work, testing, adjusting and troubleshooting guides, as well as disassembly and assembly procedures for your Caterpillar. CAT Parts Manual PDF The CAT PDF parts manual has exploded views of all serviced parts on Dust control system maintenance and troubleshooting,Troubleshooting the system. Regularly inspect the system, just as you do with other equipment, to make sure it is operating properly. Check not only the obvious things, such as fan drive belts and bearings, but also check for a plugged cyclone, a wornout elbow, a pluggedup duct or hood. Many of these problems will affect the amount of suction
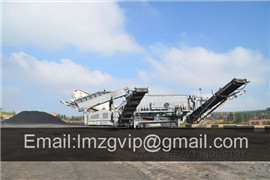
Troubleshooting And Maintenance Of Mill cafebliss.in
1022 Mill Maintenance Methods Miller Magazine. Small amounts of costs for maintenance can prevent the mill from far reaching breakdowns and a huge financial damage Besides regular maintenance on machines also decrease spare part and service costs We can diagnose many problems in the mill at early stages thanks to maintenance. Mill Maintenance Grain Milling Solutions,1230 This technique of mill maintenance allows monitoring of equipment and machines to detect possible breakdowns. As an outcome, an unscheduled shutdown of equipment and machines, unnecessary part 17 Signs of Problems with Ball Mills: Quickly Remove ,720 Add enough oil according to the regulations, and generally, 1/3 to 1/2 of the bearing gap is more appropriate. Dredge the lubrication pipeline. Install bearings or couplings correctly. Adjust the gap between the journal and the bush. Check the oil tank in time. 6. There are regular and loud knocking sounds during operation

(PDF) A Review on Maintenance and Troubleshooting of
731 Sindhu .A. Sethu Institute of Technology. Content uploaded by Sindhu .A. Author content. Content may be subject to copyright. ResearchGate has not been able to resolve any citations for thisTROUBLESHOOTING MOLDING PROBLEMS IDI ,627 TROUBLESHOOTING MOLDING PROBLEMS Molding Guide for BMC & SMC IDI Composites International June. 407 South 7th Street Noblesville, Indiana 46060 (317) 7731766 idicomposites Page 2 / 44 • Proper maintenance of paint equipment and paint boothWay Cover Troubleshooting Guide Haas ,38 Corrective Action: Perform normal machine maintenance. Remove way cover and clean out the chips. Reassemble way cover once clean if necessary. Reinstall way cover when finished. The Way Covers
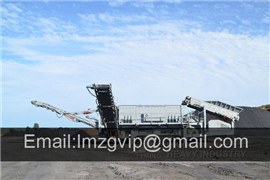
APPENDIX III: PREVENTIVE MAINTENANCE IN THE FEED MILL
29 MAINTENANCE FUNCTIONS TO BE CHECKED. Type and number of replacement parts, adequate to support an effective preventative maintenance program. Plan equipment modification, replacement or additions which will reduce maintenance and operating cost. Paint, concrete work, doors, roofs, adequate lighting, general appearance CNC Machine Checklist for Preventive Maintenance,2013626 Wipe down any stainless steel way covers and lubricate them with hydraulic oil so they move smoothly On a weekly basis, or every 40 hours, take the filter off the CNC control cabinet and clean it so air will be able to flow through for cooling. Every Three Months or 500 Hours Check and grease the chain on the chip conveyorWIRTGEN Milling Equipment Service manuals and Spare ,PDF Service Manuals, Operation & Maintenance Manuals, Spare Parts Catalogs. Site Map. How to order Diesels Machinery Auxiliary FAQ Contact/About. Write and Ask: brovertek@gmail. Cold milling machines: 6750012 1000 CBA WIRTGEN 1000 CBA Cold milling machine Spare Parts Catalog, Hydraulic diagrams, Electric Diagrams. 6750014
- محطة كسارة استخدام الحجر في اليمن
- كسارات الحجارة للتعدين
- List Of Grinding Machines Manufacturers In Peru
- مصنع معالجة الحجر المحمول
- بازیافت آسیاب تولید کننده بتن
- Cement Sand Screed Density
- إجراء الانتصاب من مطحنة الكرة
- آلة تعدين الجبس آلة كسارة الحجر
- crusher wear parts supplier
- طحن عناصر العرض طواحين الخام
- كسارة خام الحديد الفوسفور الصين
- Especialistas En Minería trituradora
- سحق مخلفات البناء المختلطة
- مصنع ماكينات الأسمنت في نويدا
- User Manual Jaw Crusher X
- تطبيق مطحنة الكرة في الصناعات
- سعر آلة تكسير الحجر 45
- عملية تخمير الكاكاو في بيرو
- أبعاد المطاحن المطرقية الجير المطفأ
- خرائط تدفق عملية التعدين