
Tube Mill Machine Rolling mill machine
25 Tube Mill or Pipe Production Line Process : Firstly, the stainless steel strips are made to go through various quality checks and are trimmed at the (PDF) Complex Numerical Analysis of the Tube ,201391 In this paper the 3D FEM analysis of basic process parameters in rotary piercing mill is presented. In this process the material is formed by (PDF) Tube hydroforming process: A reference ,2012131 by this process, tubes are formed into different shapes using internal pressure and axial compressive loads simultaneously to force a tubular blank

Simulation of tube forming process in mannesmann mill
201161 Key wordsfinite element method (FEM)–simulation–tube piercing process–Mannesmann mill Discover the world's research 20+ million members 135+ million Tube Forming Processes Pages 150 Flip PDF Download,710 About the Book Tube Forming Processes: A Comprehensive Guide This book discusses the techniques and processes of MILtube, pipe, and extrudedshape fabrication. 38 TUBE MILL Shijiazhuang FOREVER Machinery Co., Ltd,High‐frequency welded tube mill line is designed to produce round tube diameter of 10.0 38.1mm, and wall thickness of 0.4 ‐1.8mm.This line utilizes roll forming to process steel strip
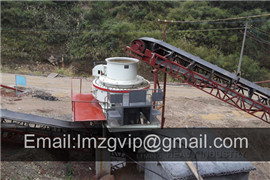
Tube Mill Machine, ERW Tube Mill Machine, Pipe Mill
The highfrequency welded pipe machine is mainly used to produce various iron pipes, carbon pipes, etc.; Stainless pipe making machine is mainly used to produce various stainless steel Tube Forming Processes: A Comprehensive Guide ,922 [PDF] Tube Forming Processes: A Comprehensive Guide (Hardback) Tube Forming Processes: A Comprehensive Guide (Hardback) Book Review Certainly, this is actually the Manufacturing Processes and Products of Steel Pipes ,43 using the Mannesmann piercing/mandrel mill process and the mediumdiameter seamless pipe mill using the Mannesmann piecing/plug mill process. The smalldiameter mill

Tube Forming AMPCO METAL
1129 Tube forming means the process of shaping a flat piece of metal into a closed tube. Compared to tube bending, where the finished tube already is enclosed, but still needs to be Tube Mill & Pipe Mill Roll Forming Machine & Tube Mill ,According to the production process of the steel pipe, the tubes can be further divided into seamless steel tubes and welded steel tubes. While the seamless steel tube can be divided into hot rolling and cold rolling (pull) two kinds, the welded steel tube can be divided into a straight welded steel tube and spiral welded steel tube.Tube Forming AMPCO METAL,1129 Tube forming means the process of shaping a flat piece of metal into a closed tube. Compared to tube bending, where the finished tube already is enclosed, but still needs to be bent into the final shape. Both, tube forming and tube bending, are metal forming processes. Tube manufacturing and profile manufacturing

Tube and Pipe Mills Formtek
For the last 60 years, Yoder has developed and continually refined their Cold Reducing Tube Mill technology for small diameter tubing. The Yoder W15S Cold Reducing Tube Mill System welds a tube up to 1.25″ (31.8 mm) diameter and can produce finished diameter down to 3/16″ (4.76 mm) diameter.38 TUBE MILL Shijiazhuang FOREVER Machinery Co., Ltd,38 TUBE MILL Φ38 Tube mil lLine High‐frequency welded tube mill line is designed to produce round tube diameter of 10.0 38.1mm, and wall thickness of 0.4 ‐1.8mm.This line utilizes roll forming to process steel strip into various shapes.Simulation of tube forming process in mannesmann mill,201161 Key wordsfinite element method (FEM)–simulation–tube piercing process–Mannesmann mill Discover the world's research 20+ million members 135+ million publications 700k+ research projects Join.

ERW Tube Mill Line Electric resistance welding
The tube is produced by the Electrical Resistance Welding (ERW) of the longitudinal seam. By using a precoated steel strip [zinc coating (galvanized), aluminum coating (aluminized), or Zn/Al Alloy Coating], a Solving problems on the tube mill The Fabricator,2001816 Tube marking in the fin section and weld box can be caused by: Overly wide strip. Driven roll settings adjusted too tight. Unparallel driven rolls. Loose driven stands. Driven rolls not set at metal line. Drive RPM not coordinated with the breakdown and sizing RPM. Fin blade worn beyond tolerance. Overly wide side roll settings.Reliablequalitytubemilltoolingforyourtubingmills,The tube mill rolls/roller/tooling's job is to take a continuously coiled flat strip, form it so that the two edges come together, hold the edges in place while they are welded by HF technology, and then size and straighten the finished tubular product to the required specifications, such as rectangle, square, Z, T, L sections and other profiles.

ERW Steel Tube Mill Pipe Making Machines New Victor
TUBE MILL FORMING & WELDING & SIZING SECTION This is the core part of the tube mill production line, which completes the transformation from strip steel to steel pipe, and determines the size and shape of the pipe FLYING SAW CUT OFF EQUIPMENT We have two kinds of steel pipe cut off equipment: cold flying saw and hot flying saw.METHOD OF MAKING HELICAL WELDED TUBES,2011616 FIELD: process engineering.SUBSTANCE: proposed method comprises welding strip reels by doublesided weld seam to form the tube with making first seam on butted edges of strip on one side in lower position and, making second seam on the other(PDF) Tube hydroforming process: A reference ,2012131 Abstract and Figures. Tube hydroforming is one of the most popular unconventional metal forming processes which is widely used to form various tubular components. By this process, tubes are formed

Tube Mills designed specifically for your application from
12 We can build exactly the machine you need: Production and Product Specifications: Outside diameters from 3/16″ to 121/2″. Wall thicknesses from 0.010″ to 0.625″. Outside diametertowall thickness ratios from 6.5 to 100:1 Production speeds over 1,000 ft/min. Applications: Mechanical Tubing Hollow Structural Section (HSS) or (PDF) Complex Numerical Analysis of the Tube ,201391 Milling Complex Numerical Analysis of the Tube Forming Process Using Diescher Mill Authors: Zbigniew Pater Lublin University of Technology J. Kazanecki Abstract and Figures This paper presents.Tube Forming Processes Pages 150 Flip PDF Download,710 Tube Forming Processes8: A Comprehensive Guide Copyright © 2003 by the Society of Manufacturing Engineers Process Planning Depending on the temper, all alloys extruded as shapes or tubing, or rolled and welded into tube, are suitable for bending. Thetemper of heattreated alloys should be T6 or less; coldworkedtemper should be H

38 TUBE MILL Shijiazhuang FOREVER Machinery Co., Ltd
38 TUBE MILL Φ38 Tube mil lLine High‐frequency welded tube mill line is designed to produce round tube diameter of 10.0 38.1mm, and wall thickness of 0.4 ‐1.8mm.This line utilizes roll forming to process steel strip into various shapes.Simulation of tube forming process in mannesmann mill,201165 The numerical model is described with taking into consideration thermal phenomena in metal during forming. The simulated results visualize dynamic distributions of mean stresses, temperature, velocity and shear stresses, especially inside the workpiece. On the basis of the basic parameters, the phenomenon in the piercing process is analyzed.Tube and Pipe Mills Formtek,For the last 60 years, Yoder has developed and continually refined their Cold Reducing Tube Mill technology for small diameter tubing. The Yoder W15S Cold Reducing Tube Mill System welds a tube up to 1.25″ (31.8 mm) diameter and can produce finished diameter down to 3/16″ (4.76 mm) diameter.

ERW Tube Mill Line Electric resistance welding
The tube is produced by the Electrical Resistance Welding (ERW) of the longitudinal seam. By using a precoated steel strip [zinc coating (galvanized), aluminum coating (aluminized), or Zn/Al Alloy Coating], a Reliablequalitytubemilltoolingforyourtubingmills,The tube mill rolls/roller/tooling's job is to take a continuously coiled flat strip, form it so that the two edges come together, hold the edges in place while they are welded by HF technology, and then size and straighten the finished tubular product to the required specifications, such as rectangle, square, Z, T, L sections and other profiles.METHOD OF MAKING HELICAL WELDED TUBES,2011616 FIELD: process engineering.SUBSTANCE: proposed method comprises welding strip reels by doublesided weld seam to form the tube with making first seam on butted edges of strip on one side in lower position and, making second seam on the other
- وظائف النفط غير الماهرة
- آلة مصانع الاسمنت في عمان
- كسارات الصابورة في السودان
- الغرينية محطة غسيل الذهب
- قطعات یدکی چرخ چرخ در ایالات متحده است
- كسارة مطحنة الأسطوانة معدات الخرسانة
- تهتز معدات الشاشة الصناعية
- أكبر شركات تعدين المنغنيز وخام الحديد في مصر
- نوعية جيدة من آلات القسم رقيقة في مصر
- مورد خام النحاس في تنزانيا
- استفاده از غربال در اوج کارخانه سنگ شکن
- كسارات الجبس في السعودية
- Small Ore Crusher Plant Supplier
- gravel crusher machine ethiopia
- سعر آلة صنع الرمل الجزائر
- تكلفة مصنع إعادة التدوير
- سحق ن راجو السوق في الهند
- مصنع تكسير خامات التربة النادرة
- stone crusher pics in large size
- استفادة منخفضة من خام الحديد